At Exterior Technologies Group, we are dedicated to providing high-performance exterior cladding solutions that emphasize durability, sustainability, and design flexibility.…

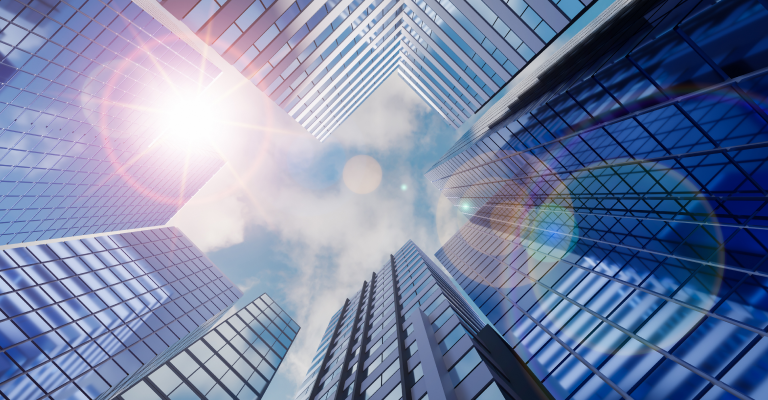
Categories: elZinc , EPD , exterior cladding , green building , sustainable cladding
At Exterior Technologies Group, we are dedicated to providing high-performance exterior cladding solutions that emphasize durability, sustainability, and design flexibility.…
Click Here To Read The Full Article
Categories: architectural innovation , cladding solutions , sustainable design
At Exterior Technologies Group, we specialize in high-performance exterior wall cladding solutions that redefine durability, sustainability, and design flexibility. As…
Click Here To Read The Full Article
Categories: EPD certification , exterior cladding , ForMe Design , SKIN Battens , Sustainable Architecture
Exterior Technologies Group is proud to offer ForMe Design's EPD-certified SKIN Battens range, a benchmark in sustainable architectural solutions. This…
Click Here To Read The Full Article
Categories: Architecture , Building Design , exterior cladding , Sustainable Construction , TAC 2.1
Unlock the potential of your projects with innovative solutions from Exterior Technologies Group. We are committed to delivering cutting-edge products…
Click Here To Read The Full Article
Categories: architectural design , exterior cladding , ForMe , Sustainable Materials , wood grain aluminum
The demand for materials that blend aesthetic appeal with functional performance is higher than ever in architectural design. At Exterior…
Click Here To Read The Full Article
Top Challenge: Balancing Aesthetics with Durability and Efficiency Architects and specification writers often struggle to find cladding materials that do not…
Click Here To Read The Full Article
Knotwood soffits are more than just a finishing touch for your home – they offer a blend of style and…
Click Here To Read The Full Article
In the lofty heights of mountainous regions, zinc roofs have become a common sight. As you ascend, zinc becomes the…
Click Here To Read The Full Article
Setting the Stage: The Moody Center's Grand Debut In the heart of Austin, the Moody Center emerged as a beacon of…
Click Here To Read The Full Article
Elevating Las Vegas with CityCenter Las Vegas in the U.S. state of Nevada, known for its constant pursuit of bigger, brighter,…
Click Here To Read The Full Article
elZinc® is a premium product, irrespective of its final application. The expectation is to achieve, in terms of product and service,…
Click Here To Read The Full Article
Sustainable building envelopes have long been at the forefront of construction innovation, with a primary focus on reducing heat loss…
Click Here To Read The Full Article
Crafted by John Wardle Architects, Curtin University's School of Design and the Built Environment (DBE) boasts a cutting-edge design in…
Click Here To Read The Full Article
elZinc is excited to announce the launch of one of the largest photovoltaic plants in Asturias, Spain. This solar generation…
Click Here To Read The Full Article
elZinc and MAZZONETTO have jointly announced a new distribution partnership for the Italian market. A distribution agreement has been formalized…
Click Here To Read The Full Article
elZinc, a renowned brand in the world of high-quality zinc products, is delighted to announce that it has secured the…
Click Here To Read The Full Article
Roofing materials are always a popular topic in Canada, and for good reason. Specifiers in the Great White North are…
Click Here To Read The Full Article
The construction of a new entrance, cycle hub and platform canopies at a popular south London train station is being…
Click Here To Read The Full Article
Kalzip is well known for their Roof and facades products made of Aluminium. In most cases, the products are used…
Click Here To Read The Full Article
Such a symbol of carbon-neutral construction. Opened at COP15 in 2009, the Zero Emission House in Copenhagen is a perfect…
Click Here To Read The Full Article